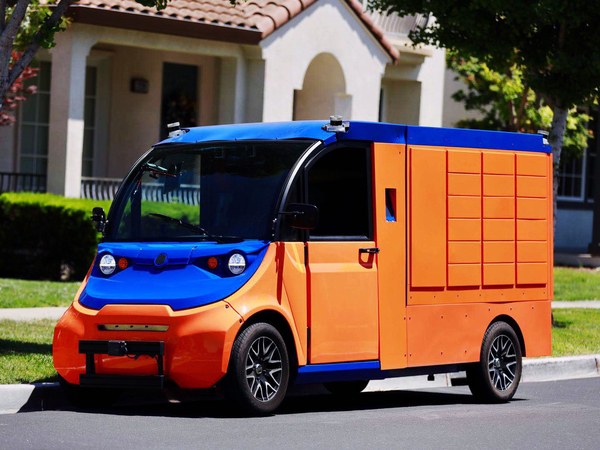
By Alex Davies
We’re a few minutes into a short drive around Oakland’s Jack London Square neighborhood, a place of wide streets and old warehouses, when we hear a metallic bang behind us. Dhruv Raturi gives me a quizzical look and shrugs. He’s sitting behind the wheel but isn’t working the steering wheel or pedals. The blue and orange Polaris GEM maintenance vehicle is driving itselfusing the suite of radars, cameras, and ultrasonic sensors. After a few turns and some yielding to pedestrians, we end up where we started. Austin Oehlerking and Mark Godwin are waiting for us in front of the warehouse out of which they run Boxbot.
Climbing out of the vehicle, I walk to the cargo box behind the two seats, bright orange and about the size of a walk-in freezer, capable of holding 63 cubic feet worth of packages. From the side, it resembles the array of mailboxes in an apartment building. I punch a code into an iPad-sized screen. The door to one compartment swings open, revealing nothing inside. That explains the mid-ride clattering: The tray holding “my” package slipped from its bracket, landing one bracket down. It’s a minor hardware malfunction, the sort common to prototypes like this. But it’s just one of many issues Boxbot’s team will have to resolve if they’re going to complete the complex, ambitious mission they’ve set themselves: remaking the way packages travel the “last mile” to their destination.
As shopping increasingly becomes e-commerce, last-mile delivery has gotten ever trickier. It accounts for up to 25 percent of the total cost of shipping. Amazon has trained customers to expect their packages in a day or two—if not faster—pushing competitors to match its speed. Many packages are destined for urban areas, where factors like toll roads, congestion, and getting into apartment complexes can make shipments more expensive. That’s why Amazon, Alphabet, UPS, and others are developing delivery drones, why veterans of Google’s self-driving car team are now making delivery-focused cargo vehicles, why the sidewalks of Berkeley, Washington, DC, and other cities are populated with delivery robots.
Thursday, Boxbot announced the first step in its own, more holistic solution: a deal with shipping company OnTrac, as a contractor using five human-driven delivery vans to move hundreds of packages a week between the depots where they’re plopped en masse by trucks, and the homes and offices where their recipients await them. Oehlerking and Godwin, veterans of Tesla and Uber, respectively, founded the company in early 2016, landed Toyota AI Ventures as an investor, and have hired about 30 people. They’ve raised $9 million to date, according to Crunchbase.
The startup is handling OnTrac’s packages for roughly one zip code in Oakland, but it plans to quickly ramp up its capacity and territory—and to attack every front of the last-mile war. Oehlerking and Godwin intend to use autonomous vehicles everywhere they can, to save on driver costs. The compartments of their delivery vans are modular, so they fit packages of just about any size.
On routes that involve more complex driving or toting a package to a doorway, Boxbot will send a human, but the cofounders expect smart routing and dispatch software to make life on the road more efficient. Walking to a customer’s front door might involve opening a gate, climbing a stoop, moving around a flower bed, or tucking a package where it can’t be seen from the street—things robots are just no good at. “That last 50 feet is not going to be automated for a very long time. Definitely not in the next five years, probably not in the next 10,” Godwin says. “Even 20 years from now, human beings will be involved in the process. They’ll just be significantly more productive.”
Finally, they promise a loading system that uses new software and hardware to sort packages and put them in just the right spot in just the right vehicle. The executives are quiet about how that will work exactly, but they say their system will save precious time both in the warehouse and on the road.
“Our view is, keep the parts of the system that are still working,” says Oehlerking, Boxbot’s CEO. For everything else, they’ll look for any improvement possible. They hope that with a variety of upgrades, they can squeeze more money out of a traditionally low-margin business.
The multifaceted business plan is smart, says Anne Goodchild, who runs the Supply Chain Transportation and Logistics Center at the University of Washington. “It’s great that they’re thinking about multiple strategies, and that one size doesn’t fix all.” Solely removing the driver won’t make the last-mile business easy or profitable, she says. “We call them drivers, but they’re actually delivery workers,” Goodchild says. “And for a tiny fraction of the time, they’re moving their little mobile warehouse.”
It’s a lot to take on for a small company. The big self-driving outfits employ thousands, the small ones at least a few dozen. The 30 or so Boxbotters have to make a vehicle drive itself, design a new system for automatically loading vehicles, create software to make routing and dispatch more efficient, all while making actual deliveries. More people and more money will surely help. And if they can only make one part of this equation work, Boxbot could become a nice acquisition target for a bigger player.
The startup has, at least, chosen an appropriate place to give it a shot. The Oakland warehouse it occupies was once home to the Kellogg Express Company, which in 1919 the Oakland Tribune praised for swapping out horse-drawn carriages for a fleet of “autocar trucks,” letting it make its deliveries faster and more efficiently than ever.